Контроль качества сварочных работ
Опубликовано: 06.09.2018
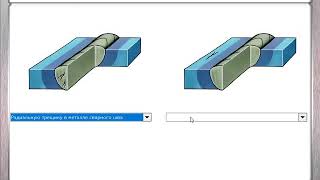
Контроль сварочных работ – гарантия высокого качества сварных металлоконструкций
Сварочный процесс может осуществляться разными способами и материалами. Сегодня одним из наиболее перспективных способов считается механизированная сварка в защитном газе. В качестве защитного газа может использоваться как один определенный газ, так и смеси газов. Подробнее о видах и особенностях механизированной сварки в среде защитных газов и идет речь в статье.
Одним из наиболее перспективных видов сварки является механическая сварка в защитном газе. Использование углекислого газа в качестве защитного в сварочном производстве, его преимущества и недостатки – то, о чем мы расскажем Вам в этой статье.
Механизированные способы сварки осуществляются с использованием специальной порошковой проволоки в качестве расплавляющего материала (т.е. вместо электрода). Эта статья рассказывает именно о порошковой проволоке: о свойствах, способах ее использования, особенностях.
Дефекты сварных соединений
stalevarim.ru
Что говорит РД о контроле качества и сварке?
08 января 41 просмотров 46 рейтингОглавление: [скрыть]
Глава 1 и глава 2 Содержание 3 и 4 глав Глава 5 и глава 6 Глава 7 и глава 8 Глава 9 и глава 10РД сварка регламентирует все нормативы проведения такого рода работ, так как многие нормативно-технические документы потеряли свою актуальность при смене социально-экономической системы и переходе на рыночную экономику. С его помощью ведется контроль качества сварки.

Руководящий документ содержит в себе требования к основным видам сварки, обработке металла и контролю качества сварки.
Весной 2001 г. в Российской Федерации принят руководящий документ, регламентирующий выполнение сборки металлоконструкций методом сварки в области промышленности и строительства (в определенных кругах именуемый как РД о сварке). В документе указаны основные требования к следующим видам сварки:
электрическая сварка электродами с защитной обмазкой вручную; сварочные работы в среде защитного газа и процесс получения неразъемного соединения проволокой с применением защитного порошка в полуавтоматическом режиме; механизированная и автоматизированная обработка металла под флюсом; регламентирован контроль качества сварки.Руководящий документ состоит из десяти глав, каждая из которых регламентирует правила на определенном этапе выполнения сварочных работ. В конце документ содержит 17 приложений со справочной информацией и образцами оформления различных документов при выполнении работ.
Глава 1 и глава 2
Квалификационная схема подготовки персонала сварочного производства.
В главе 1 в первом разделе изложены общие требования к проектированию и выполнению монтажных и строительных работ с применением сварки металлоконструкций. Указаны все необходимые дополнительные документы, правилами которых нужно руководствоваться при работе.
Второй раздел этой главы устанавливает правила определения квалификации сварщиков, необходимый объем знаний в области техники безопасности и работы на механизированных и автоматизированных сварочных установках. Сварка и контроль пробного образца являются необходимым условием при устройстве на работу.
Определены основные требования к руководящему персоналу и работникам, выполняющим контроль качества сварочных швов. При контроле сварки пробного образца предъявляются требования, как к готовому изделию.
Правила разработки проекта производства работ определены в разделе 1.3. Разработка проекта должна выполняться с учетом современных технологий, обеспечивающих оптимальные сроки и способы монтажа. Указаны основные параметры оборудования для электроснабжения и требования по снабжению строительных и сборочных площадок горючими газами и кислородом.
Основные требования к качеству основных материалов для сборки и его контролю определены в главе 2. В ней предусмотрен порядок освидетельствования материалов, не имеющих сертификата качества.
Вернуться к оглавлению
Технические требования и аттестация процедур сварки металлических материалов.
В главе 3 указаны требования к качеству материалов, используемых при сварке, и правила испытания материалов и сварных соединений, выполненных с применением этих материалов при отсутствии документации. Проверке и испытаниям должны быть подвергнуты следующие материалы:
электроды для ручной дуговой сварки; проволока для сварки со всеми предусмотренными в ППР видами защиты; защитные, горючие газы и кислород; флюсы, используемые согласно ППР при автоматизированных и механизированных сварочных работах.Для всех материалов в соответствии с установленным производителем сроком годности должен быть составлен график проверки и необходимых восстановительных операций. Регламентируются правила временного хранения, проверки и подготовки материалов перед использованием и требования к баллонам для газов.
Все требования к оборудованию для выполнения всех сварочных работ, используемому для контроля качества работ, и дополнительному контрольно-измерительному оборудованию, не входящему в комплекты основного, определены в главе 4. РД определяет правила первичного осмотра и проверки оборудования при поступлении от поставщика, правила ежедневной проверки и осмотра перед началом работ. Указаны правила периодической поверки измерительных приборов и оборудования в соответствии с указанным производителем сроком, список необходимой документации. Для оборудования, используемого в дефектоскопии, указаны правила и порядок проверки и настройки приборов после ремонта и поверки, а также определена необходимая квалификация персонала, выполняющего эти работы. В разделах 4.8-4.10 определены области использования сварочного оборудования в зависимости от рода тока и степени автоматизации работ. Технические характеристики оборудования указаны в приложениях 9-12.
Вернуться к оглавлению
Рисунок 1. Пример акта на прокалку электродов.
Пятая глава устанавливает правила контроля и подготовки материалов к сборке. В ней определены порядок устранения дефектов материалов, способы зачистки кромок сварных швов, методика сборки изделия на временные сварные соединения (прихватки). Регламентированы основные методы перемещения и кантовки изделия, собранного на временных соединениях, дана методика проварки временных соединений при нанесении основного шва. В приложении 13 указаны наиболее распространенные приспособления, используемые для фиксации, стягивания и растяжения собираемых конструкций, а также способы их крепления на поверхностях деталей.
Технология окончательной сварки собранных конструкций и необходимые условия для выполнения работы регламентированы в главе 6. В первом разделе этой главы рассмотрены основные методы наложения шва при сварке конструкций из различных сталей и с разнообразной конфигурацией. В ней определены способы возобновления сварного соединения после остановки. В таблицах указана температура наружного воздуха, при которой допускается выполнять сварку различных марок стали без предварительного подогрева.
В разделах 6.2-6.4 рассмотрены аналогичные вопросы применительно к каждому конкретному виду сварки (с ручной, автоматизированной или газовой защитой). Для каждого вида работ рекомендованы оптимальные режимы с указанием сварочных материалов, силы тока, положения электрода и других параметров.
Вернуться к оглавлению
Рисунок 2. Бланк товарно-транспортной накладной.
В главе 7 рассматриваются способы сварки наиболее употребляемых конструкций, оптимальные методики наложения сварочных швов, их последовательность.
Приведены примеры следующих конструкций:
укрупнение двутавровой балки; удлинение подкрановой балки; изготовление верхнего узла фермы с усилением; сварка соединения фермы при использовании парных конструкций; изготовление узла фермы при облегченной конструкции; соединение колонны из двутавровой балки; конструкция стыковки балки перекрытия и колонны.Показаны некоторые методики изготовления часто используемых конструкций с применением автоматизированных сварочных устройств. Все рассмотренные методы показаны на чертежах с указанием порядка наложения швов и необходимых приспособлений и условий при работе.
В первом разделе главы 8 определен порядок надзора во время процесса сварки (от начала до окончания).
Второй раздел главы 8 определяет условия внешнего осмотра шва с использованием измерительных приборов необходимой точности и применение методов ультразвуковой дефектоскопии или радиографии при необходимости, определяемой проектной документацией. Вместо измерительных приборов допускается использование специальных шаблонов. В приложении 14 приведены требования, которым должно соответствовать качество сварных соединений, и допустимое количество дефектов на определенной длине шва.
Вернуться к оглавлению
Девятая глава определяет правила и методы устранения обнаруженных дефектов. В ней рассмотрены способы выборки металла в дефектных местах и приемы зачистки стыков для последующей сварки. Регламентируются условия проведения работ в регионах с температурой ниже 40° C и других климатических зонах.
Определяет количество и порядок оформления документации при выполнении сварных работ, а также перечень документов для заказчика. Стандартные формы всех документов показаны в приложении (рис. 1,2).
В приложениях содержится много необходимой информации о свойствах и механических характеристиках применяемой стали, используемых при сварке материалах, есть чертежи и схемы применяемых приспособлений, технические и электрические данные оборудования для сварки и контроля сварки.
Это руководство предназначено для специалистов, исполнителей и руководителей монтажных и строительных работ.
expertsvarki.ru
Контроль сварочных работ
Подробности Подробности Опубликовано 25.05.2012 16:03 Просмотров: 21521Страница 1 из 7
ПОРОКИ СВАРНЫХ СОЕДИНЕНИИ
Высокое качество сварных изделий должно повседневно обеспечиваться тщательным и всесторонним контролем всего сварочного производства, начиная от контроля свариваемого металла, электродов, сварочной проволоки и флюсов, и кончая контролем самого процесса сварки и готовой продукции. Кроме ого, необходимо к выполнению сварочных работ (особенно ответственных) допускать только подготовленных сварщиков, прошедших соответствующие испытания (см. приложения). Все контрольные функции выполняются на предприятиях обычно отделами технического контроля. Но ответственность за качество продукции не снимается с работников, занятых в сварочном производстве и, в первую очередь, со сварщиков. Именно от сварщика, его квалификации во многом зависит качество сварных изделий. Главная задача контроля качества сварки сводится к выявлению пороков в сварных соединениях и устранению их. Пороки могут быть наружные и внутренние. К наружным порокам относятся: 1) неравномерное сечение шва по ширине и толщине; 2) несоответствие фактически выполненных размеров шва запроектированным в чертеже или ТУ; 3) подрезы кромок основного металла; 4) незаделанные глубокие кратеры швов; 5) пористость наружного слоя шва; 6) наплавы металла и нечистая поверхность шва; 7) наружные трещины в шве и основном металле. К внутренним порокам относятся: 1) непровар по кромкам основного металла; 2) несплавление валиков при многослойной сварке; 3) наличие шлаковых включений; 4) внутренние газовые поры; 5) внутренние трещины в шве и основном металле. Наружные пороки выявляются при осмотре сварной конструкции после зачистки швов. Внутренние пороки выявляются с помощью просвечивания рентгеном (рентгенографированием) и лучами радиоактивных элементов (гаммографированием), магнитным и ультразвуковым контролем, металлографическим анализом и механическими испытаниями образцов, изготовленных из наплавленного металла и сварных соединений.
НАРУЖНЫЕ ПОРОКИ СВАРНЫХ ШВОВ
Неравномерное сечение шва по толщине и ширине. Этот порок часто встречается при ручной дуговой сварке у малоквалифицированных сварщиков, не освоивших равномерное поступательное движение электрода с поперечным колебательным двигателем. Отклонения в размерах швов: а - неравномерно сечение; б - несимметричность (ширина больше высоты); в ослаблено рабочее сечение; е - несоответствие профиля шва заданном); на чертеже.
Кроме того, неодинаковая ширина шва получается при плохой подготовке кромок, наличия неравномерных зазоров, неправильного подбора режима сварки, а также плохого формирования шва, вызванного ослаблено качеством покрытия электродов. При автоматической сварке основной причиной неравномерного сечения шва является неравномерный скос кромок. Неравномерные швы создают некрасивый внешний вид всей конструкции в целом. Несоответствие размеров шва запроектированным в чертежах. Несоответствие размеров обычно снижает механическую прочность сварных соединений и подлежит исправлению. Этот порок встречается обычно при сварке внахлестку. При стыковых швах и швах внахлестку наружные размеры определяются толщиной свариваемых кромок. Швы уменьшенного против указанного на чертеже размера должны исправляться дополнительной подваркой. Увеличение размеров швов против заданных нежелательно, так как это ведет к излишним внутренним напряжениям и деформациям и удорожает, сварку: увеличивается расход электродов, электродной проволоки и флюсов, электроэнергии и затраты рабочей силы на сварку.
Подрезы на валиковых швах; б - на стыковых швах. На многих заводах считается допустимым при приемке швов больших сечений отступление от заданных размеров в сторону уменьшения на 1 мм, а в сторону увеличения на 2 мм. Фиг. 105. Подрез, образующийся при неточном направлен и электрода в случае сварки валиковых швов под слоем флюса в нижнем положении. Подрезы. Подрезами называют продольные углубления, образующиеся в основном металле по краям шва (фиг. 104). Подрезы получаются вследствие применения слишком большой силы тока при неправильном ведении процесса сварки. Подрезы - опасный и серьезный порок в сварных изделиях, так как они ослабляют сечение основного металла в наиболее опасной переходной зоне. Кроме того, подрезы, вызывая резкую местную концентрацию напряжений, могут служить причиной появления трещин. Избежать подрезов можно путем правильного подбора режима сварки, внимательным наблюдением за движением электрода, а также выбором наиболее удобного для сварки положения шва в пространстве. Исправляются подрезы наложением тонкого шва электродом малого диаметра. Подрезы могут получаться при автоматической и полуавтоматической сварке под слоем флюса валиковых швов в нижнем положении. Основной причиной подрезов в этом случае является смещение электрода в сторону вертикальной кромки. Незаделанные кратеры получаются в результате небрежного и неумелого выполнения сварки. В месте кратера толщина шва резко уменьшается, что вызывает понижение прочности сварного соединения. При действии динамической нагрузки разрушение шва почти всегда начинаетсяс кратера, поэтому кратер необходимо обязательно заделывать. При сварке изделий из низкоуглеродистой стали заделка кратера может осуществляться как на самом шве, так и с выводом его на основной металл. На легированной стали кратеры должны заделываться только непосредственно на швах во избежание возникновения трещин в основном металле. Как уже отмечалось в главе VI, при автоматической сварке кратеры выводятся на специальные выводные планки. Пористость наружного слоя шва и внутренние газовые поры. Пористость в швах образуется при наличии газов, не успевших выделиться из жидкого металла при его быстром остывании. Причин образования пористости швов следующие: а) загрязнение свариваемой поверхности или электродной проволоки, маслом, краской, а также повышенная влажность покрытия или флюса. за повышенная скорость сварки на загрязнение свариваемой поверхности или электродной проволоки ржав иной, маслом, краской, а также повышенная влажность покрытия или флюса, повышенная скорость сварки, при которой ускоряется процесс затвердевания наплавленного металла и одновременно задерживается выделение газов; недостаточная раскисленность, насыщенность газами или окислами основного металла. Швы с большим количеством пор имеют низкую прочность и под ежат обязательному исправлению путем вырубки и повторной заварки металла находилась более продолжительное время в жидко сварку производить только по чистым кромкам; наложение шва вести с такой скоростью, чтобы ванна расплавленного металла находилась более продолжительное время в жидком состоянии. Для этого рекомендуется производить кольцеобразные и петлеобразные возвратно-поступательные движения концом электрода; электроды и флюсы перед свар ой необходимо прокаливать, Наплывы и нечистая поверхность шва. При быстром расплавлении электрода наплавленный металл местами переполняет ванну и, растекаясь, застывает на основном металле, образуя местные наплывы. Наплывы могут быть в виде отдельных капель, иногда наплывы имеют значительную протяженность. При сварке под слоем флюса наплывы часто наблюдаются у валиковых швов, свариваемых в нижнем положении. Нечистая поверхность шва с каплями (брызгами) расплавленного металла и частицами шлака от покрытия непосредственно не оказывает отрицательного влияния на прочность шва, но указывает на небрежное выполнение и возможность существования внутренних пороков. Швы необходимо защищать от остатков шлака, брызг металла при помощи зубил, остроконечных молотков или других инструментов.
Наплывы при сварке валиковых швов; б - при сварке стыковых швов; при автоматической сварке, образующиеся из-за смещения электрода на верхний лист. Высокую производительность труда и хорошее качество обеспечивает очистка швов с помощью пневматических. Трещины при сварке од флюсом в валиковом шве. электрических машинок с закрепленной на валу стальной щеткой. Наружные и внутренние трещины. Трещины в шве - один из самых опасных пороков, снижающих механическую прочность сварных изделий и зачастую делающих их непригодными к эксплуатации. Трещины в швах образуются под действием внутренних термических напряжений, которые возникают при неравномерном нагреве и охлаждении сварных конструкций в процессе сварки. При сварке легированных сталей, чувствительных к закалке, помимо этого возникают также напряжения, вызываемые изменениями структуры. Совместное действие термических и структурных напряжений делает сварку легированных сталей более опасной в отношении образования трещин. Трещины в стыковых швах образуются чаще, чем в валиковых. На валиковые швы термические напряжения влияют значительно меньше. Различают трещины продольные и поперечные. Продольные трещины возникают чаще всего в кратере, а затем распространяются вдоль шва. В кратере металл при охлажден и испытывает растягивающие напряжения и более загрязнен вредными примесями, снижающими его пластичность. Поперечные трещины образуются преимущественно при сварке легированных сталей. Причем они часто располагаются на основном металле® зоне закалки, где пластично понижена. Помимо видимых (наружных) трещин, встречаются невидимые волосные трещины. Эти трещины особенно опасны, так как не могу быть обнаружены невооруженным глазом, Невидимые трещины чаще всего появляются на границе | сплавления наплавленного металла с основным из-за наличия с напряжений. В утренние пороки сварки в виде непровара невидимых частей, чаще всего появляются на границе сплавления наплавленного металла с основным из-за наличия ряжений. Внутренние пороки сварки в виде непровара кромок, крупных газовых пузырей или шлаковых включений так могут быть причиной возникновения трещин. На образование трещин оказывает сильное влияние избыточное содержание вредных примесей в наплавленном металле - серы и фосфора. Сера приводит к образованию «горячих трещин», образующихся при температуре выше 500-600°, а фосфор «холодных», образующихся при температуре ниже 500-600°.ба с трещинами сводится к получению наплавленного металла с повышенными пластическими свойствами. Необходимо также соблюдать правильный режим сварки, при котором с трещинами сводится к получению наплавленного металла с повышенными пластическими свойствами. Необходимо также соблюдать правильный режим сварки, при котором усадочные напряжения будут минимальными.
electrowelder.ru
Контроль сварочных работ - Cварочные работы
При сварке соединений арматуры и закладных деталей железобетонных конструкций осуществляют входной, пооперационный и приемочный контроль.
Качество подготовки арматуры и элементов закладных деталей к сварке и качество их сборки проверяют периодически, но не реже двух раз в смену путем осмотра и соответствующих обмеров. Рекомендуемый режим сварки проверяют на пробных образцах. Производятся осмотр, обмер и механические испытания сварных соединений пробных образцов, выполненных на выбранном режиме. Условия сборки и сварки пробных образцов должны соответствовать аналогичным условиям основных сварных соединений. Контроль качества сварных соединений в процессе их изготовления осуществляется также не реже двух раз в смену осмотром и обмером швов и соединений. Для этого выбирают три сварных соединения, худшие по внешнему виду. Размеры проверяют металлическим измерительным инструментом или специальным шаблоном, обеспечивающим измерение с погрешностью не более 1 мм. Смещение осей стержней в стыковых соединениях определяют с помощью рейки и линейки. Рейка должна иметь вырез для обхода утолщения металла шва или накладки в месте стыка (рис. 74). Металл шва осматривают с помощью лупы с не менее чем 5-кратным увеличением. Сварные соединения не должны иметь видимых при внешнем осмотре трещин, скоплений и цепочек пор, шлаковых включений, резких сужений и перерывов. Переход от наплавленного металла к основному должен быть плавным без подрезов основного металла. Все кратеры должны быть заварены. Сварочные работы, прерванные при обнаружении дефектов в сварных соединениях, можно продолжить только после выяснения и устранения причин их возникновения.
Рис. 74. Схема определения положения осей арматурных стержней в стыковых сварных соединениях 1 — линейка; 2 —рейка; е — смещение осей стержней
Качество сварных соединений при приемочном контроле определяют по результатам их осмотра, обмера и механических испытаний на прочность контрольных образцов этих соединений. Механическим испытаниям на растяжение подвергают три контрольных образца, которые отбирают в произвольный момент времени и вырезают из сварных соединений конструкций, выполненных последними к моменту отбора образцов. Вместо вырезанных образцов можно использовать «образцы-свидетели», которые должны быть сварены в модели стыка и извлечены из нее для испытаний. Модель стыка изготовляют по проектным размерам стыка конструкции. Соединения в модели стыка и сварку соединений в конструкции выполняет тот же сварщик, в том же пространственном положении и с применением тех же режимов, материалов и оборудования. По требованию приемщика на участках, где после внешнего осмотра предполагается наличие дефектов, осуществляют контроль засверли-ванием швов для выявления внутренних дефектов. Шов засверливают по его оси с углублением в основной металл на 1,5 мм. Диаметр сверла берут на 2—3 мм больше ширины усиления шва. Если в результате засверли-вания будут обнаружены недопустимые внутренние дефекты, по предполагаемым границам сомнительного участка шва нужно сделать два дополнительных засвер-ливания. При удовлетворительном качестве удаляют участок шва между засверленными отверстиями. В случае установления даже одним из дополнительных засвер-ливаний неудовлетворительного качества шва засверли-вание продолжается до установления фактических границ дефектного участка. После устранения дефектов участок вновь засверливают.
Устранять дефекты рекомендуется следующим образом. Швы с непроварами, порами и шлаковыми включениями удаляют на длину дефектного участка и заваривают вновь. Перерывы, ослабления швов и кратеры заваривают. Стыки со вздутием в верхней части шва, выполненного ванным способом, вырезают и снова заваривают. Подрезы основного металла зачищают и заваривают.
При проверке качества стыковых соединений одиночных стержней, выполненных ванной, ванно-шовной сваркой и многослойными швами, механические испытания контрольных образцов на прочность можно заменить ультразвуковой дефектоскопией соединений.
Читать далее:
Сварочные флюсыСварочные электродыОбщие сведения о сварке арматурыПротивопожарные мероприятия при сваркеБезопасность труда при сварке технологических трубопроводовБезопасность труда при сварке строительных металлических и железобетонных конструкцийЗащита от поражения электрическим током при сваркеТехника безопасности и производственная санитария при сваркеУправление качеством сваркиСтатистический метод контроляstroy-server.ru